Survey: Barnacle fouling is a significant problem for shipowners
When participants of the recent “Coatings’ key role in shipping decarbonisation” webinar were asked to rank if hard biofouling, such as barnacle fouling, was a problem on a scale from being no problem at all to being a huge problem, 53% of attendees confirmed that hard biofouling is a “significant problem”, with a further 27% describing it as a “huge problem.”
In fact, only 2% of the 200 respondents to the interactive, live survey run during the webinar, hosted by Riviera Maritime in late November, thought that hard biofouling was ‘no problem at all’.
In this blog you will gain in-depth insights from a recent webinar on advanced hull coatings, dive into the challenges and hull biofouling and explore how coating innovations are driving improvements in fuel efficiency and emissions reduction.

Antifouling coating specific webinars and conferences always attract a large audience, and this webinar was no different. 371 registrants received a series of short presentations from the expert speakers, Markus Hoffmann, Technical Director at I-Tech, Carl Barnes, General Manager – Marine Consulting at Safinah Group and Nikolaj Malmberg, Head of Global Business Development, Marine at Hempel, followed by an interactive survey and a question-and-answer session. Click here to view the presentations made during the webinar.
Overall, the aim of the webinar was for expert panelists and participants to examine the impact of advanced hull coatings on fuel efficiency and emissions reduction and the role that antifouling coatings play in meeting meet IMO EEXI, CII and other emission reduction regulations. The webinar also provided a porthole for participants to look into emerging trends and R&D in sustainable marine coatings.
The participants for this webinar were mainly charterers, shipowners and shipyards with a sprinkling of antifouling coating companies, biocide suppliers, academia and regulators.
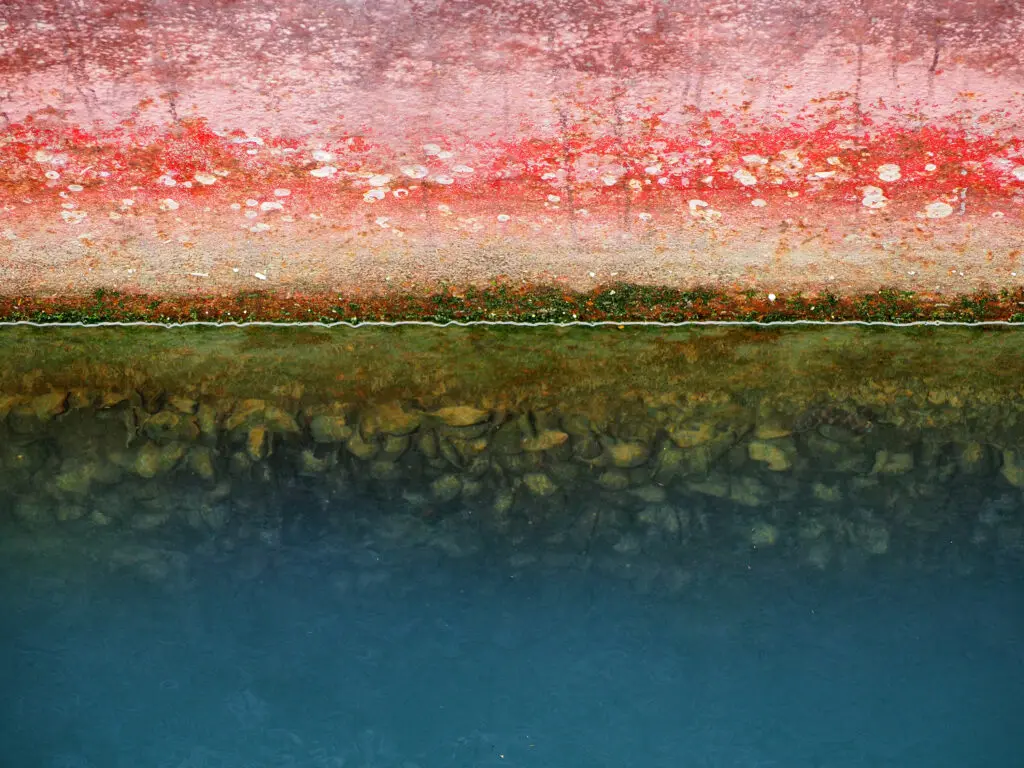
The survey – who took part?
To start, let’s take a look at the people who were actually surveyed. Data collected by Rivieria Maritime for the webinar shows us that there was a significant presence of technical decision-makers across a mix of predominantly vessel operators, technology providers, and regulatory bodies from all around the world.
From the ship owning and operating, chartering and ship management companies present, roles included:
- Technical Directors, Naval Architects, Fleet Technical Managers, Performance Specialists, Technical Superintendents, Fleet Managers, Managing Directors and Operations Managers.
From the antifouling technology companies, biocides suppliers, consulting companies and academia, roles included:
- Scientists, Chemists, Research & Development, Chief Scientists, Business Development, Sales Managers, Marketing Managers and Commercial Directors
The survey – what did they say?
Through interactive forums and mini market surveys like this, the antifouling coatings sector can really understand the challenges faced by ship owners and/or operators and shipyards, especially when 84% of the people surveyed said they are exploring alternative methods/technologies for combating biofouling.
Let’s take a look at a quick summary of responses to the survey.
🔹 Biofouling Solutions: When asked if they were exploring alternative methods/technologies for combating biofouling, an overwhelming 84% of participants said yes, highlighting the need for innovative technologies (such as Selektope) in the market to address biofouling in a sustainable way.
🔹 Top Priorities for Choosing Coatings: When asked what the most important factor when adopting new antifouling technologies is, better performance metrics (39%) and cost-effectiveness (26%) were ranked as the most critical factors, indicating the industry’s dual focus on technical and financial feasibility. This was followed by regulatory compliance (20%) and environmental impact (15%).
🔹 Sustainability is Important: When asked if they agreed or disagreed with the statement ‘Maritime Sustainability is a Main Criterion for Underwater Coatings selection’, 39% of respondents said that they mostly agreed, followed by 34% who fully agreed. 18% of participants took a neutral standpoint on the statement and 8% mostly disagreed with the statement.
🔹 The Prominent Future Technologies in Antifouling: when asked what they thought would be the Prominent Future Technologies in Antifouling, most respondents (67%) believe that the future of antifouling lies in using a combination of multiple technologies. 17% of participants selected highly engineered coating systems only, 14% selected hull cleaning solutions only and finally, 3% selected advanced monitoring systems only.
🔹 Hard Fouling = Hard Problem: when asked to rank hard fouling, including barnacles, on a scale from being no problem at all to being a huge problem, 53% of attendees expressed that hard fouling is a significant problem, with 27% of respondents describing it as being a “huge problem.” These findings underline the urgency of ensuring continuous active protection against barnacle fouling, in particular, in underwater hull coatings.
🔹 Selecting coatings: part supplier recommendation, part cost-dependent: when asked to indicate how they select antifouling coatings, participants confirmed that paint supplier recommendation was the most common method for selection among the group (35%). This was followed byselection based on cost (25%), use third party advice (21%) and continue with previous product/supplier (19%).
🔹 Underwater cleans – what’s the frequency?: when asked how often hull cleaning is conducted during a 5-Year Dry Dock Cycle, almost half of the participants surveyed selected the option ‘every 1 – 2 years’ (45%), whereas 34% of respondents confirmed that they conducted hull cleaning only ‘1 or 2 times’ during the full dry dock period. Equally 11% of respondents said that they clean every 6 months, and 11% said that they never clean at all.
Questions to the experts
The webinar sparked questions to flow in from participants about antifouling coatings, hull cleaning challenges, antifouling technology and biocides. Performance validation, environmental impact, adoption challenges, and technical considerations were also hot topics, all answered by the panel of antifouling coating experts.
In this part of the blog, we present some of the questions that were asked. If you would like to read the transcript of the full question-and-answer session, click here
Do Air lubrication systems affect antifouling coatings?
Firstly, the interaction between coatings and air lubrication technology was addressed, with Markus Hoffmann (I-Tech) confirming that since air lubrication systems are not running constantly, when the airflow stops the fouling control systems should work normally. There is no indication that the air lubrication systems affect the efficacy of hull coatings as long as the air used is clean and not contaminated.
Do current Volatile Organic Compounds (VOCS) measurement protocols miss critical emissions?
VOCS came up, with a question of what evidence indicates current VOC measurement protocols might miss critical emissions. Markus Hoffmann (I-Tech) confirmed that for fouling control systems, the VOC very often is not measured like in other areas like plastics but calculated on the amount of VOC being part of the paint formulation from the very beginning. These values of the initial VOC concentrations is then confirmed by standardized test methods, he confirmed.
How do you quantify the economic impact of biofouling?
The question was asked, ‘how do you quantify the economic impact of that 0.5mm slime layer across different vessel types and operating profiles?’. Carl Barnes (Safinah Group) provided the clarification that the economic effect always depends on vessel type, speed, activity and roughness including slime. The studies from the US Navy for one of their frigates at 15 knots, for example, that indicates an increased shaft power of 9 % for light slime, he said. He also pointed to the latest IMO study Impact of Ships’ Biofouling on Greenhouse Gas Emissions states an impact of light slime from 3 to 20%.
Dry docking interval standards, coatings pre-planning and inspections
Following Safinah Groups’ presentation on in-docking inspections and findings, the question ‘How do your findings on coating degradation rates question current dry-docking interval standards?’ was put to Carl Barnes (Safinah Group). His answer was that Safinah Group’s data on coating degradation typically shows that extensive pre-planning prior to dry docking is not being carried out. For example, incomplete / inaccurate vessel data, changes to the operating profile, not considered fleet-wide specifications, no diversification and a lack of structured test patching etc.
Hull cleaning intervals – how to work out when is best
The question ‘What evidence suggests current cleaning interval recommendations might be based on flawed assumptions?’ was answered by Carl Barnes (Safinah Group), he gave the advice that whenever a clean is being considered, an inspection should be carried out first to determine the level of fouling. Any underwater clean will (no matter how carefully managed) cause some level of damage to the fouling control coatings (scratched, DFT loss etc).
Are biofouling risk assessments flawed?
The question ‘What patterns in your dataset suggest current biofouling risk assessments might be fundamentally flawed?’ was answered by Carl Barnes (Safinah group) who stated that Safinah’s data suggests that it is a lack of extensive pre-planning and a ship-specific approach to specification and selection that is often the cause of fouling issues.
Why choose the same coating, even if performance was poor in the past?
The question of ´why do vessels often select the same manufacturer despite poor performance´ was asked to the panel, Carl Barnes (Safinah Group) answered, stating it´s actually difficult to answer, but perhaps it may be historical (it’s what we have always used), it´s because of a relationship with a particular paint supplier, budget considerations or confusion due to a complex product range (150+ products).
Do current coating performance metrics need to be revised?
The question was put to the expert panel of what evidence indicates current coating performance metrics might need fundamental revision. Markus Hoffmann (I-Tech) stated that it is difficult to quantify the performance of fouling control coatings under controlled laboratory or immersion testing. As a consequence, there is no general accepted standard (like ISO) to measure the performance of an antifouling. The best ways to analyse the performance is either via indocking data and or performance measurement methods like ISO 19030. Additionally, a challenge is that the fouling depends on activity, speed, fouling pressure and on biological processes. To get reliable data one needs larger numbers. Methods like ISO 19030 have some challenges like the separation of the propeller from the hull. At the same time these data are not publicly available, and not all coating systems are being tested.
Microplastics and marine coatings
The topic of microplastic emissions from marine coatings came up in the question ‘What data suggests current microplastic regulations might miss critical environmental impacts?’ Markus Hoffmann (I-Tech) said that generally, all regulatory bodies regulate their specific field not taking into account a holistic picture. Many stakeholders of the coating industry work to further reduce the emissions of microplastic into the sea. Generally, microplastic particles are not added into paints and the emissions coming from hull coatings is very small compared to other sources. As the positive impacts of hull coatings like fuel savings are not fully taken into account there is a significant risk that this can lead to higher emissions of particles into air which can end up in the sea.
The solution for stationary vessels in tropical waters
The question ‘What would be your solution against biofouling for a stationary vessel in tropical waters?’ was answered by Markus Hoffmann (I-Tech) who advised that if the vessel will be stationary for very long period it will be difficult to protect it from fouling. For longer periods generally high performing antifouling coatings with a higher polishing rate and if it is barnacle fouling, a coating containing Selektope.
Our conclusion
The interactions during this webinar from participants through the survey and question-and-answer session confirm that advanced antifouling technologies play a crucial role in achieving decarbonisation targets. Also, there is great appetite for existing and new solutions that combat biofouling, particularly for owners and/or operators looking to meet regulatory requirements around ship efficiency and emissions reduction.
To address the issue of hard fouling, active protection through antifouling coatings, such as those containing Selektope, is essential for the complete prevention of barnacle fouling. The responses to the survey conducted during this webinar confirm the necessity of incorporating Selektope into antifouling coatings, by doing so, barnacles will be effectively prevented from attaching to ships protected by Selektope.
————–
Click here to watch the full recording of the webinar.
Click here to read the full transcript of the question-and-answer session.
Click here to find out more about the upcoming International Antifouling Conference 2025.
Related articles
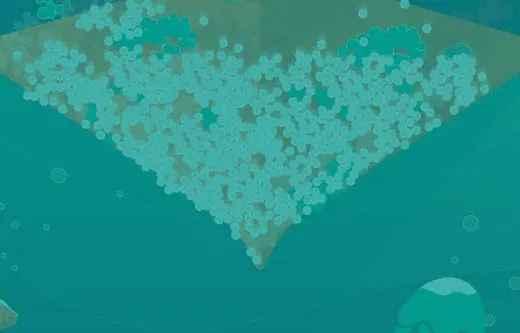
Fascinating facts about barnacles: how they attach to ship hulls?
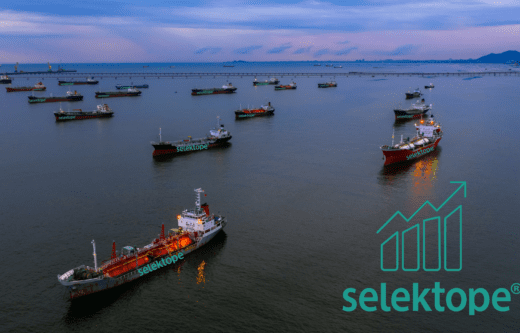
20 tonnes of Selektope safeguards 2,500 vessels from barnacles
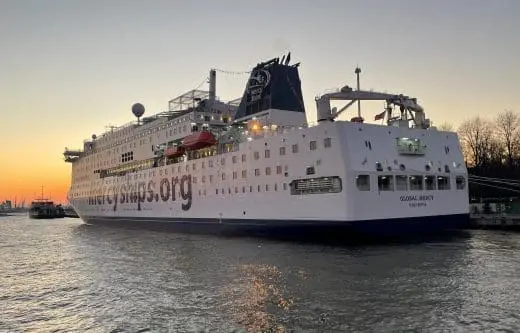
Insights from our time spent on the world’s Largest Hospital Ship
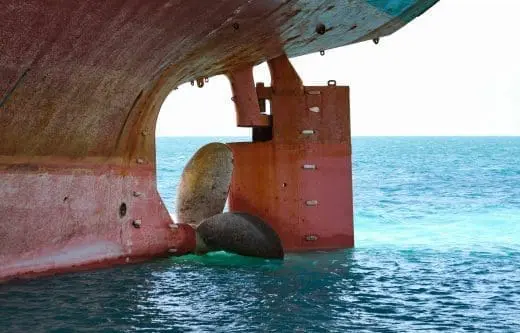